From Concept to Creation: Inside the World of Cutting-Edge Molds and Dies
- Lokesh Modi
- /
- June 28, 2024
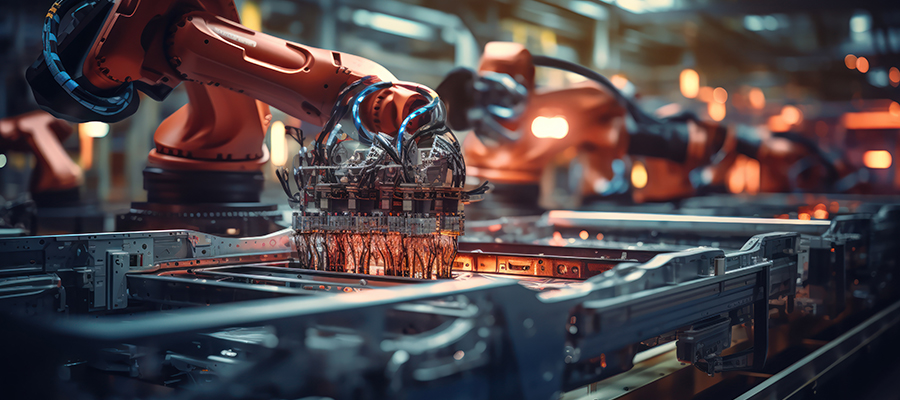
Creating high-quality molds and dies is a meticulous process that requires a blend of innovation, precision, and expertise. Fenestec has established itself as a leader in this field, providing top-tier solutions for various industries, including switchgear and plastic industries. In this blog, we will take you through the fascinating journey from concept to creation, showcasing the cutting-edge technologies and methodologies that make Fenestec a standout in the industry.
Initial Concept and Design
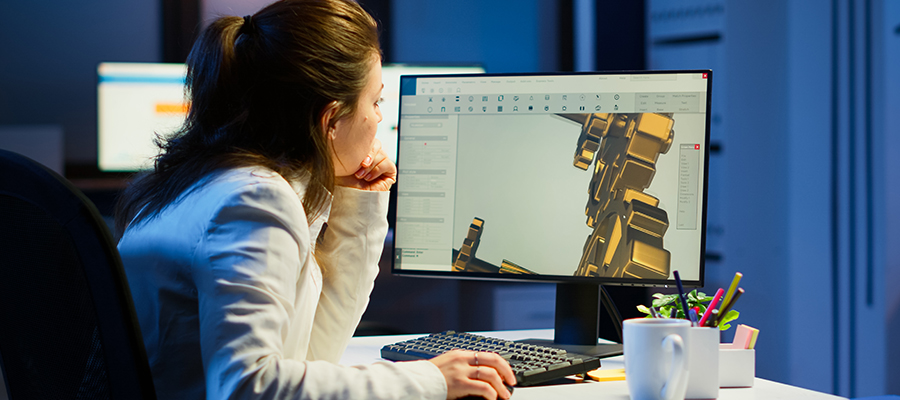
The journey begins with a concept. Clients from various sectors, such as the plastic and switchgear industries, approach Fenestec with their unique requirements. Using advanced CAD software, engineers translate these concepts into detailed designs. This step is crucial as it lays the foundation for the entire manufacturing process.
Prototyping and Testing
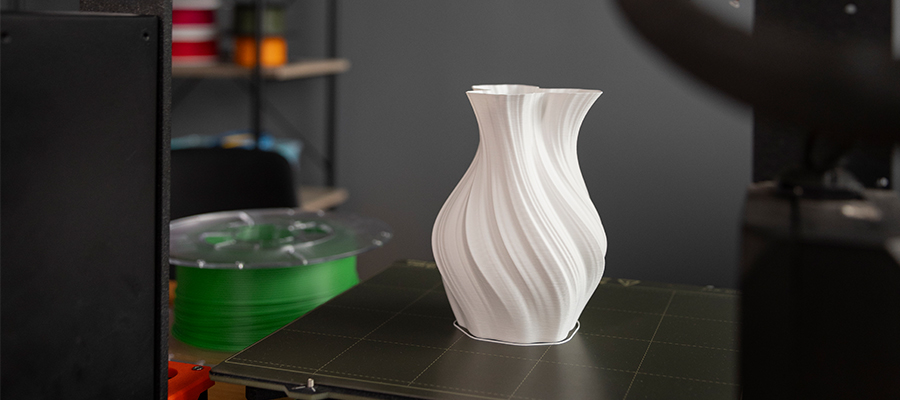
Once the design is finalized, the next step is prototyping. Rapid prototyping techniques, such as 3D printing, allow for the creation of accurate models quickly. These prototypes are then subjected to rigorous testing to ensure they meet all specifications and standards. This stage is vital for identifying any potential issues before mass production begins.
Precision Manufacturing
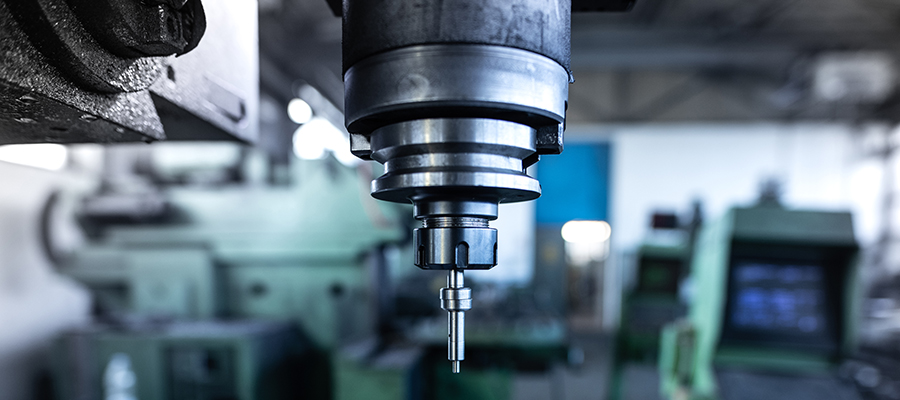
With a validated prototype in hand, the focus shifts to manufacturing. Fenestec utilizes state-of-the-art CNC machining centers and EDM (Electrical Discharge Machining) to produce dies and molds with unparalleled precision. These technologies enable the creation of complex geometries and fine details that are essential for high-performance components.
Quality Assurance
Quality assurance is a cornerstone of Fenestec's manufacturing process. Each mold and die undergoes thorough inspection using advanced metrology tools, ensuring that every dimension and feature meets the highest standards. This meticulous attention to detail is particularly important in industries like switchgear, where even minor deviations can impact performance and safety.
Applications in Various Industries
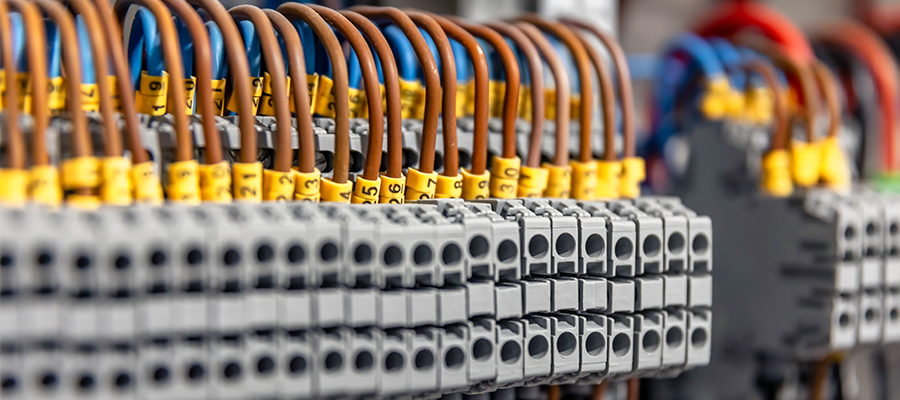
The molds and dies created by Fenestec find applications in a wide range of industries. In the plastic industry, they are used to produce everything from everyday household items to specialized components for medical devices. In the switchgear industry, precise molds are essential for manufacturing parts that ensure the safety and reliability of electrical systems.
Continuous Improvement and Innovation
Fenestec is committed to continuous improvement and innovation. By staying at the forefront of technological advancements and industry trends, the company ensures that it can meet the evolving needs of its clients. This commitment to excellence has earned Fenestec a reputation as a trusted partner in the manufacturing sector.
Conclusion
From concept to creation, the process of manufacturing high-quality molds and dies is complex and requires a blend of innovation, precision, and expertise. Fenestec's commitment to excellence and its use of cutting-edge technologies ensure that it can deliver top-tier solutions for industries like switchgear and plastics. As the demand for high-quality components continues to grow, Fenestec remains dedicated to pushing the boundaries of what's possible in mold and die manufacturing.